“Dye proves a connection between two points… nothing more, nothing less”
Each year, thousands of dollars are spent on dye tests. The person demanding the dye test is requiring someone else to spend their money. Usually the person making the demand is more concerned about protecting his company’s investment (and his career) than protecting you, the home buyer! If you’re told to “get a dye test,” you better understand what it can and can’t do, and what it will and won’t tell you. Read on, and when you’re through, tell your “dye test advisor” to read this as well.
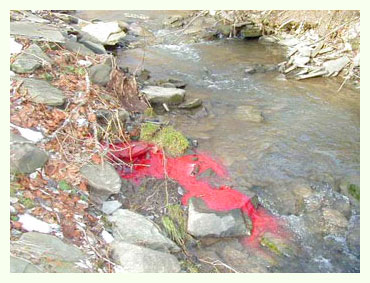
If you’re buying or selling a home with an onlot sewage disposal (septic) system, you better find out what type of system is buried in the yard before you sign on the dotted line. More and more home sellers are finding that financial institutions routinely ask for a “dye test” in order to reach some conclusion about the health, operation, condition or mere presence of an onlot sewage disposal system (septic system). Most frequently, a system inspection is sought prior to a land sale. And just as frequently, the service request is received only a few days before settlement – when the pressure is on to close the deal. If you’re the buyer, you want to make informed decisions without last minute pressures. If you’re the seller, you want to make a full disclosure of ALL you know about the system. Two simple steps will make these things possible, but more on that later.
There are two basic techniques used to evaluate onlot wastewater treatment systems. In the dye test method, a non-toxic colorant is introduced to the system. Then, the evaluator walks the property looking for signs of the dye. The other method is a comprehensive onlot wastewater treatment system inspection done in accordance with the Inspection Standards developed by the Pennsylvania Septage Management Association.
Misplaced confidence
Relying on a dye test to evaluate an onlot wastewater treatment system’s condition is like relying on the drips on the garage floor to evaluate the mileage performance of the car that usually parks over the drips. Intuition tells you the drips came from the vehicle. You are clueless about what part of the vehicle originated the drips or if that part is working properly. You can only assume there is a connection between the vehicle and the drips. That’s about all a dye test proves . . . that there is a connection between the point where the dye is introduced into a piping system and the location where it is visible. No more, no less.
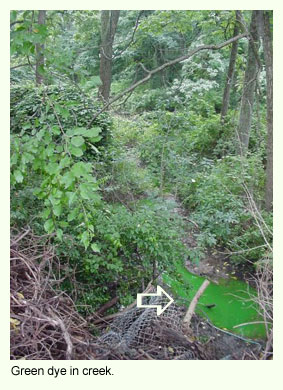
Relying on a dye test to determine the size and condition of the treatment tank (or even if there is one), the size and type of the absorption area (if any), or its location or condition yields no valid conclusions if all you do is introduce dye and look for its appearance. Since the typical retention time in a 1,000 gallon treatment tank is about three days, you better not base any conclusion on what you don’t see the same day you introduce the dye. But, you better look, for if there is a surface discharge, it may not linger three days. Likewise, if you don’t look in the right places, you may never see the dye even though it has surfaced.
An onlot wastewater treatment system inspection performed by a PSMA/NOF-certified inspector will include a thorough examination and evaluation of every component of the system. The size, type and condition of the treatment tank will be documented. The system’s maintenance history will be researched and the location of all major components will be discovered and documented. Most importantly, the Inspector’s report will indicate Unsatisfactory conditions which may signal problems before they reach the stage of a “regulatory” malfunction. Unsatisfactory conditions which indicate the system or a component is not performing as intended will be noted and reported.
A regulatory malfunction occurs when the system discharges untreated or partially treated sewage to the surface of the ground or the waters (above or below ground). The municipal regulatory official (in PA, its the Sewage Enforcement Officer or SEO) should be contacted if a malfunction is detected. Remedial measures consistent with a government issued permit must be taken. In this situation, it is the landowner’s responsibility to contact the regulatory official. A conclusion that a system is unsatisfactory may not immediately require intervention by the regulatory official.
An Unsatisfactory system or component may continue to “work” for some time. It may also fail in a few days if the volume of waste it is expected to handle changes drastically. If, for example, a middle-aged couple has successfully used the system and the property is about to be purchased by a similarly situated couple, it may continue to perform satisfactorily. On the other hand, if a young couple with four children will be moving in, the system’s successful days may be fewer than the number of new occupants!
In this situation a dye test would very likely reveal “no problem,” yet a regulatory malfunction could develop after the new owners move in. Were the dye test’s results right or wrong? In the absence of a surface discharge or subsurface linkage to a well, seeing no dye and concluding the system was working was a correct assumption. Unfortunately, there was no system inspection, and the soil masked all indications of a potential problem.
Select the Proper Tool
What went wrong in this example? It’s simple, the evaluatory tool selected (dye test) was not the right tool for the job. If a pipe was suspected of discharging sewage to the road ditch, or a pipe to a stream or even a wet spot in the yard, a dye test could be the right tool to prove or disprove your suspicions. The right tool in this example, however, is a PSMA/NOF onlot wastewater treatment system inspection which would have revealed the hidden problems of the failing system.
Lenders and buyers get squeamish when they hear “failing system.” Buyers must make decisions that are difficult at best. The buyer and lender want an assurance that the system will work. The system evaluator cannot give one, only a professional judgment of the system’s current condition and, at best, an indication of the likely outcome of continued use. The SEO, by law and regulation, cannot evaluate systems in his or her jurisdiction as part of a land sales transaction for the buyer or seller, and he is not able to change or undo the inspector’s conclusion.
Is the lender truly being duly diligent in demanding a dye test, or merely searching for a dye test report to hide behind and a warm-blooded scapegoat in case the onlot system fails? What is the benefit to the new owner if the system passes the dye test and fails the test of everyday use? And if the system fails, is the lender really in a better position than if no test had been done? Indeed, Commonwealth Court has already described the PSMA/NOF Inspection Standards as “the industry standard.” Be sure to select the right tool to evaluate an onlot wastewater treatment system. Clearly, you do not want to be forced to answer this question: “Why did you select a dye test when you knew a more accurate testing tool was available?”
Read more about dye testing in PADEP’s Fact Sheet about Dye Tests as well as Penn State University’s Extension’s Fact Sheet about the use of dyes and tracers to confirm septic failures.
To locate a PSMA/NOF-certified onlot wastewater treatment system inspector, search our member directory.